Cedar Classical
The head veneer is made up from the off-cuts of the back, so there is no need to worry about whether or not it matches and I’ve carried on the “green” motif with a strip down its centre, as Hauser used to. The purflings around the top edge will also match: attention to detail is what counts!
The back has its decorative strip in place. I use 0.6 mm boxwood veneer for these lines and the back and side purflings. Boxwood has a very dense grain, its main use, used to be for wooden printing blocks, I guess the close grain means that when you print, you don’t get the texture of the grain showing. That’s a similar reason for me using it, when you sand and finish the rosewood, its purple dust and resin, doesn’t discolour the boxwood, so you get really clean lines.
You can see the rosette, back and head veneer in the picture below.
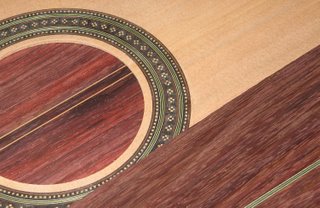
I’ve just bought myself a new plane, a Veritas low angle bevel up smoothing plane. It works so well on the type of wood that I use.
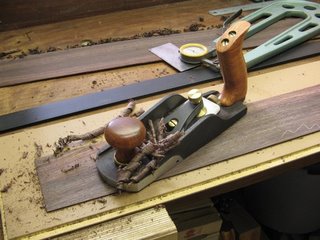
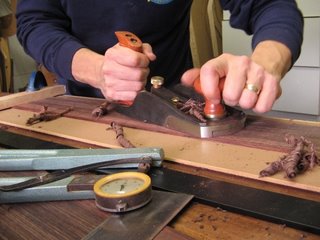
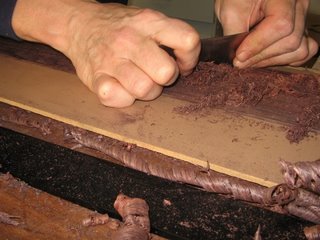
The guitar’s sides are bent, I use a hot iron (it’s actually aluminium). I love the idea of getting solid wood and bending it by hand to get the shape; the smell of the resins and the steam rising and the guitar’s shape appearing is almost magical.
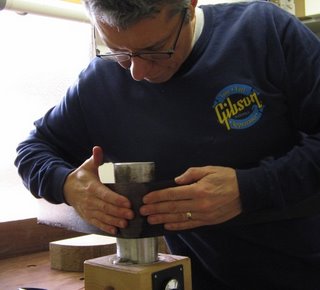
After the sides, the end blocks are glued in place. I use a mahogany block for where the neck joins. I make the neck separately and use a dovetail to join the two component parts. I feel that I can work with greater accuracy this way. Although this is not regarded as the Spanish method of building, Ignacio Fleta, probably one of the greatest Spanish luthiers, used this method.
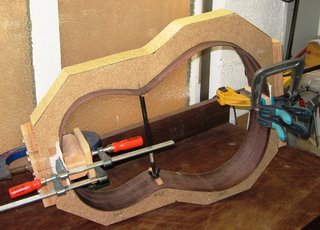
0 Comments:
Post a Comment
<< Home